Robotics Implementation in Kitopi
- malaikarehman6
- Apr 26, 2023
- 4 min read
Updated: Apr 27, 2023
By Cecilie Twisttmann, Robotics System Designer
As part of Kitopi's mission of continuing to be the technological frontrunner in the food delivery industry, Kitopi has invested in end-of-line robotic systems for the Satellite Kitchens (SKs) to aid in the sorting and packing of product items.
The robotics system is being developed and tested in the Danish Robotics R&D subsidy. The pilot version of the system is to be deployed and tested in DSO2 this year.
What is Robotics?
The concept of robots, or automated machines that can perform tasks without human intervention, has been around for centuries. However, the modern history of robots began in the early 20th century, with the development of technology that enabled the creation of machines that could mimic human actions.
In recent years, robots have become increasingly sophisticated and versatile, developing technologies such as artificial intelligence, machine learning, and advanced sensors.
Looking at the current trends in the robotic industry and types of robots we find 3 main topics:
Collaborative robots (cobots): Cobots are designed to work alongside humans, with built-in safety features to prevent accidents. These robots can be programmed to perform repetitive or dangerous tasks, freeing up human workers for more complex or creative work.
Autonomous mobile robots (AMRs): AMRs are self-guided robots that can navigate their environment without needing external guidance. They are used in logistics and warehousing to transport goods, and in manufacturing to move materials between workstations.
Artificial Intelligence (AI): AI is increasingly being used to improve the capabilities of robots, enabling them to learn from their environment and make more intelligent decisions. This leads to more flexible and adaptable robots that can work in a wider range of applications.
Today, robots are used in a wide range of industries, from manufacturing and logistics to healthcare, entertainment, and education.
Within recent years, robotics are being introduced in the food industry to improve efficiency, consistency, and safety. Some examples of robotics use cases within the food industry:
Automated sorting and packaging: Robots can be used to sort and package food products, such as fruits and vegetables; by size, shape, or weight. This can reduce the need for manual labor and improve the accuracy and consistency of the packaging.
Quality control: Robots can be equipped with sensors to detect defects, such as bruises or mold, in food products. This can help ensure that only high-quality products are sent to market.
Food processing: Robots can be used to perform tasks such as cutting, slicing, and dicing food products. This can help reduce the risk of injuries to human workers and improve the consistency and accuracy of the processing.
Food delivery: Robots can be used to deliver food to customers, such as in restaurants or hospitals. This can help reduce the need for human interaction and improve the speed and efficiency of the delivery process.
Food safety: Robots can be used to perform tasks such as cleaning and sanitizing equipment, reducing the risk of contamination and foodborne illness.
This robotic system, currently being designed and developed by the Danish team will be utilized for the sorting and packaging application.
The Robotic System
An in-house Kitopi Robotic Sorter system is being designed to sort prepared food items into customer orders.
The robotic sorter will contribute to the KPI for a Packing time of <2 min, which is achieved by <50-60% of the orders when the robotic project was initiated. Based on project observations, up to 50% of the current pack time today is allocated to manual sorting as the packers need to identify which order an item belongs to.
Additional Value Creation
The value creation of the robotic system lies within process optimization. Implementation of the autonomous system will impact the entire SK process as it requires streamlining current processes and will aid the workers. This will free up time for the operators, which can be used more effectively elsewhere in the process.
Furthermore, system implementation will automatically incorporate quality checks e.g. of packaging closure, and aid a bulletproof item-to-order packing. The system will facilitate higher item and time traceability during the preparation and packing as the items will be identifiable via QR codes.
By enforcing digital item ID, the margin of errors can be monitored with increased accuracy. This will enable better risk management before the item leaves the kitchen. Hereby aiding the goal of achieving high customer satisfaction.
Merging with our proprietary Smart Kitchen Operating System (SKOS)
The system will be connected to the SKOS via a Kitchen Unit Control (KUC), which will facilitate and ensure data is provided in a timely manner to the robotic system.
The merging and integration of the robotic system with existing systems - more specifically SKOS - is a combined effort across the country and teams. The teams involved in the integration include the skilled and highly experienced members from the Prototype team, which is developing the KUC, and have provided a mock-up of KUC endpoints with swagger UI for early test purposes. This team is also working on KDS front-end development for both prep and pack station KDSs.
Moreover, we have been fortunate enough to get experienced back-end developers on board from the newly established Expresso team for ticket processing integration. The teams recently had a productive 3-day hackathon in Denmark, where they had several workshops and robotic demos.
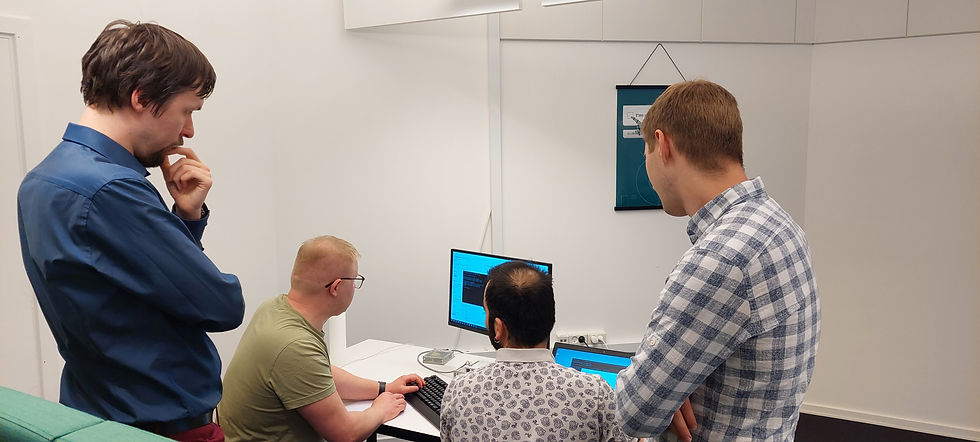
Robotic Hackathon - 04/April/2023
The output of the Hackathon has been the creation of detailed sequence diagrams for happy paths and edge cases, initial connection on the robotic system controller, and optimization of system contracts.
If you want to know more details about the robotic sorter project, please do not hesitate to reach out to the author on either LinkedIn (external) or Slack (internal).
The comment is helps to guide anyone looking for reliable and accurate legal translations in the UAE. Superior Translation offers specialized legal translation services, ensuring that contracts, agreements, and official documents are handled with precision and confidentiality. They are also recognized as a trusted certified legal translation service provider for individuals and businesses alike. On the other hand, Wadi Alhuroof provides professional legal translation services in Dubai, delivering certified solutions accepted by courts and authorities. Their expertise extends across the UAE with reliable legal translation in UAE, making them a dependable partner for both personal and corporate needs. Together, both companies ensure high-quality translations that meet official standards.
<a href="https://goldcoastclear-carts.com/product/3-100counts-300-counts-2g-live-diamonds-disposables/"rel="dofollow">3 100counts (300 Counts) 2G Live Diamonds Disposables</a>
<a href="https://goldcoastclear-carts.com/product/apple-tartz-gold-coast-clear/"rel="dofollow">APPLE TARTZ Gold Coast Clear</a>
<a href="https://goldcoastclear-carts.com/product/astro-berry-gold-coast-clear/"rel="dofollow">ASTRO BERRY GOLD COAST CLEAR</a>
<a href="https://goldcoastclear-carts.com/product/bahama-mama-gold-coast-clear/"rel="dofollow">Bahama Mama Gold Coast Clear</a>
<a href="https://goldcoastclear-carts.com/product/banana-runtz-gold-coast-clear/"rel="dofollow">Banana Runtz GOLD COAST CLEAR
</a>
<a href="https://goldcoastclear-carts.com/product/black-widow-gold-coast-clear/"rel="dofollow">BLACK WIDOW GOLD COAST CLEAR</a>
<a href="https://goldcoastclear-carts.com/product/blackberry-sour-gold-coast-clear/"rel="dofollow">Blackberry Sour GOLD COAST CLEAR</a>
<a href="https://goldcoastclear-carts.com/product/blood-orange-gold-coast-clear/"rel="dofollow">BLOOD ORANGE GOLD COAST CLEAR</a>
<a href="https://goldcoastclear-carts.com/product/bloody-mary-gold-coast-clear/"rel="dofollow">BLOODY MARY GOLD COAST CLEAR
</a>
<a href="https://goldcoastclear-carts.com/product/blue-devils-gold-coast-clear/"rel="dofollow">BLUE DEVILS GOLD COAST CLEAR</a>
<a href="https://goldcoastclear-carts.com/product/blueberries-n-cream-gold-coast-clear/"rel="dofollow">BLUEBERRIES N CREAM GOLD COAST CLEAR</a>
<a href="https://goldcoastclear-carts.com/product/blueberry-bonanza-gold-coast-clear-for-sale/"rel="dofollow">Blueberry bonanza gold coast clear for sale
</a>
<a href="https://goldcoastclear-carts.com/product/blueberry-cookie-gold-coast-clear/"rel="dofollow">Blueberry Cookie GOLD COAST CLEAR</a>
<a href="https://goldcoastclear-carts.com/product/blueberry-yum-gold-coast-clear/"rel="dofollow">Blueberry Yum GOLD COAST CLEAR</a>
<a href="https://goldcoastclear-carts.com/product/bootylicious-gold-coast-clear/"rel="dofollow">Bootylicious GOLD COAST CLEAR</a>
<a href="https://goldcoastclear-carts.com/product/bubba-gum-gold-coast-clear/"rel="dofollow">Bubba Gum GOLD COAST CLEAR</a>
<a href="https://goldcoastclear-carts.com/product/cake-popz-gold-coast-clear/"rel="dofollow">CAKE POPZ GOLD COAST CLEAR</a>
<a href="https://goldcoastclear-carts.com/product/caribbean-breeze-gold-coast-clear/"rel="dofollow">CARIBBEAN BREEZE GOLD COAST CLEAR</a>
<a href="https://goldcoastclear-carts.com/product/cemetery-kush-gold-coast-clear/"rel="dofollow">CEMETERY KUSH GOLD…
While reading about robotics innovations in Kitopi’s operations, I was reminded that technology isn’t the only force transforming lives. In India, true change often comes from compassion and care. A close friend overcame addiction with the help of rehabilitation centre Vikalp Rehab, where professional treatment meets emotional support. This trusted name in India offers personalized recovery programs, expert counseling, and a nurturing environment for complete healing. Just as robotics boosts efficiency in business, Vikalp Rehab restores hope and purpose in people’s lives, helping them start fresh with strength and confidence.
Boost your academic success with professional LAW assignment help from Assignment Mentor, offering expert guidance, thorough research, and tailored support to ensure top-quality work and improved grades in every legal subject.<a href="https://assignmentmentor.co.uk/law-assignment-help/">Professional LAW Assignment Help for Academic Success</a>
Excel in your MBA dissertation with expert UK writing help. Assignment Guidance offers tailored, plagiarism-free dissertations crafted by specialists to boost your grades and ensure your academic success.
MBA Dissertation UK – Expert Writing Help for Your Success